Conventional versus Renewable insulation
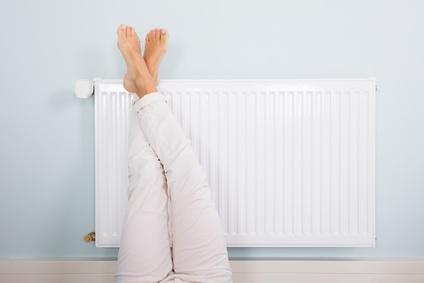
- Energy-efficient refurbishment
- Structural-physical properties of heat insulation
- Conventional insulants
- Renewable resources
- Insulating or heating?
Insulants have different purposes in housing construction. They are used for thermal insulation and sometimes to reduce footfall and impact sound. The recent shift in focus to environmental consciousness has lead to great demand for efficient building, the energy consumption for production and waste disposal of insulating material is becoming increasingly important. Bio-degradable materials gain popularity seeing that they are a “green“ choice and have astounding insulating properties.
Energy-efficient refurbishment
In the course of growing environmental awareness, many home owners have been thinking about refurbishment and insulation. Proper insulation benefits climate protection and increases cosiness of the home as well as the value of the building.
Which measures are taken?
The roof / attic storey or ceiling on above rooms with heating should be equipped with a minimum thermal insulation. You can do this by yourself or employ qualified skilled workers to do it for you. Careful works prevent future heat bridges and structural damage. Outdated radiators and boilers must be replaced.Structural-physical properties of heat insulation
Materials with low thermal conductivity are used as insulators to prevent the building from heating up and cooling down.
Coefficient of heat conductivity λ
The lower its thermal conductivity, the better the material insulates. The insulation of all materials used during construction is based on their ability to seal in air in interspaces between pores, cells or fibres. Stagnant air conducts little heat (0.024 λ). Think of hardened foam plastics or natural wooden insulators. All plant cells seal in air and that is what synthetic insulators imitate.
Glass has a value of 0.76 λ; whereas glass wool (fine glass fibres with air air in small interspaces) reaches 0.04 – 0.05 λ. Sheep’s wool scores even better with 0.035 λ – your house’s very own woolen hat.
The heat conductivity states the transmissibility for thermal flow of a material. A good insulator prevents the loss of heat energy and also ensures the building will not heat up excessively during the summer. The classification of heat conductivity shows how thick the insulating layer must be. The thickness of the insulator is determined by an energy consultant because this value depends on material, location and energy consumption of the building.
- Flammability (fire protection)
- Shape retention (moisture, temperature change, UV)
- Resistance to mould, decay, insects/animals
- Compressive strength
- Medial risk due to ingredients and gas release
- Price (in comparison with savings)
- Availability
- Moisture absorption / Balancing out humidity
- Resistance to heavy rain
- Odour, if applicable: visual nature
- Processability
- Weight
- Added benefit, e.g. sound insulation
- Renewable resources
- Energy expenditure for production and delivery
- Durability/service life
- Disposal: additional costs for disposal? Use as compost / sale?
Conventional insulants
Well-proven conventional materials used for building insulation include polystyrene, mineral wool and foam glass. These inorganic insulators can originate from minerals (glass and rock wool as well as clay and volcanic rock) or they are made artificially from crude oil. A popular petroleum product is expanded polystyrene (EPS).
Expanded polystyrene (EPS) has a thermal conductivity of 0.035 to 0.050 λ and a cheaper purchase price. Inserted into boards, EPS is available in many DIY and hardware stores and is easily installed by users themselves. It is highly in demand by building owners who are looking to refurbish the structure because it is very easy to process.
The material is impenetrable by moisture which in turn has its benefits and drawbacks. If water vapour accumulates inside the house, the risk of mould growth increases considerably. Otherwise this foam insulation does not soak up outdoor moisture and rain water. The place of installation is a crucial factor, if you are living in areas with frequent floodings, EPS boards are a sensible choice. However, EPS has its limits and is not very suitable for insulation on the outside of the building because it reacts to UV radiation and begins to tear.
What is worth mentioning is the poor protection against fire this material provides. Starting from temperatures of a little more than 100°C it begins to burn and release toxic fumes. The front of the Grenfell Tower block in London was insulated with composite panels with a core made of plastics. In June 2017 a devastating fire spread in the upper storeys of the building and claimed about 80 people according to the ongoing investigation. The flames quickly grew because melting material drips down and allows the fire easy passage to the top. This incident caused debates about the petroleum materials used for insulation and cladding in general.
To reduce flammability, the flame retardant HBCD is added to EPS boards. However, this substance releases seriously toxic gas when burning which has a long-lasting effect on waters and organisms.
Styrofoam boards and environmental safety are not compatible with each other. Woodpeckers often mistake the hollow sound of the exterior insulation finishing system with rotten wood and begin pecking holes. Not only does this damage the look of the building, but also gives moisture and insects the chance of infiltrating the building substance. Furthermore, heat insulation in these spots neutralised in these spots.
Mineral wool made of molten fine-grained stone or glass has a better environmental balance. The process of melting requires the most energy. The melting turns the material into a well insulating, low-priced substance that is not flammable under “normal” temperatures and less susceptible to mould and moisture. The tricky part is the processing during construction. Old mineral wool with a fibre thickness below 3 micrometres can break and cause fine dust. The dust is resirable and can cause cancer. Since 1996 thicker fibres are being produced that might lead to irritation upon direct contact with the skin, however it is harmless to the lungs. Nevertheless caution is advised, protective clothing should always be worn, particularly during refurbishment and deconstruction of old buildings.
Renewable resources
Using bales of straw or hemp as a modern insulant? It sounds odd if you first hear about it. Natural insulators are made from plant or animal tissue such as sheep’s wool, cork, timber or flax. Their insulating properties are equal to classic products made from crude oil or minerals, jute for example has a rating of 0.037-0.040 λ. The natural fibres also have a more pleasing visual nature than Styrofoam and rock wool. Recycled materials like cellulose from used paper also insulates well (0.039 to 0.045 λ). It is resistant to a maximum temperature of 60°C. In combination with façade cladding the fire hazard will not increase. The classification of flammability of ecologic insulating materials ranges from non-combustible with flammable elements (wood wool) to normal combustible (Styrofoam). Compared to conventional raw materials natural fibres grow back and have an even CO2 balance. Only the transport from countries abroad has an influence on the energy use, for example a fictitious company in Estonia importing cork from Portugal. Plants like flax and hemp are naturally resistant to pests and can be grown in fields. In some cases, certain agents (salts, plant starch or polymers) are added to the natural materials to increase stability and protection against fire. If that is not the case, the insulants are compostable after finishing their service life.
Natural insulators made of cellulose are sold in a loose form and are used to plug, injected/filling insulation or as pre-fabricated boards.
Benefits of egological insulants
- Sustainable, renewable
- Positive eco and energy balance
- Often short transportation routes, local cultivation
- Low thermal conductivity
- Non-hazardous
- Regional materials can be used
- Recycling of old newspapers, use of wood shavings, etc.
- Sometimes sound-insulating
- Acceptable fire classification
- Partially naturally resistant to vermin and fungi
- Pleasant smell (except maybe cork)
- Little to no chemical pollution
- Slip-proof, homelike structure
The consumption of embodied energy required for manufacturing, transportation and disposal of natural insulators is considerably lower.
Our conclusion:
The area of the building in contact with the earth is quite moist, that is why natural insulators are often not suitable. Synthetic or mineral insulants are more appropriate for perimeter insulation, foam glass for example. The other levels of the building like the roof or indoor insulation can be equipped with a wide selection of natural materials.
Natural building materials like timber and cellulose fibres balance out moisture (capillary active). This reduces the risk of mould growth in the house. Other insulants react more intense to moisture and change their shape when damp. Water has a thermal conductivity of 0.58 Λ meaning damp materials insulate less efficiently than dry materials. Mineral wool and glass wool are other examples for inferior perimeter insulants.
Conventional insulators incorporate a steam brake/vapour barrier made of sheet to prevent humidity from the building from infiltrating the insulation material where it would condensate to water. The sheets are mounted to the heat insulation facing to the inside of the room. Aluminium-clad insulation is another conventional vapour barrier. Plaster made from lime or loam is the natural equivalent. The structural conditions on-site determine the most suitable material.
The acquisition costs for ecological insulation is occasionally higher than polystyrene board or other conventional material. On the other hand, renewable materials are often compostable after their service life, meaning you do not have to deal with disposal fees.
⮊ Choose builders with experience in ecologic insulation material.
Insulating or heating?
Retrofitting the building envelope results in tremendous costs in most cases which rarely pays off compared to the estimated reduction of heating costs. Particularly the use of insulating foil or adhesive board is often criticisied by experts. After extensive calculations by an independent energy consultant, under consideration of resale value etc. the decision to just keep on heating possibly is more favourable from an economic point of view than investing in thermal insulation. However, ecological thinking is important to cut carbon dioxide emission. An efficient (new) heating system such as a pellet stove is a great alternative for old buildings with insufficient insulation.
Did you know?
One way of reducing heating costs despite insufficient insulation is use a ceiling fan with a winter setting. Warm air always rises upwards and accumulates at the ceiling, it does not stay on the ground. That is why the floor always seems to be cold in winter no matter how much you turn up the radiator or fuel the fireplace. A ceiling that runs in reverse disperses the layer of heat on around the ceiling and recirculates it in the room. The warm and cold air mix, the indoor temperature evens out and cold spots are eliminated without any unpleasant draught.
The costs for a fan and the installation thereof are quite favourable. DC motor fans only consume between 3 and 35 depending on the speed setting. The majority of the devices requires no maintenance at all and comes with a motor warranty of up to 25 years. Furthermore, many ceiling fans incorporate a light kit and can be used instead of a normal light fitting.